冶金行业系统解决方案
原料厂基础自动化控制系统
能够为钢铁企业提供原、燃料工程散状物料处理、分类堆放进行先进的自动化控制技术,为多胶带机、大型斗轮机、卸料机、取料机设计合理工作流程,有效提高企业的原料进料出料系统管理。
- 火车受料系统
- 一次堆取场系统
- 二次堆取场系统
- 配料混合系统
- 原料输出系统

烧结厂基础自动化控制系统
通过原来场进料,发挥现有设备的最大潜力为前提,高效、可靠的生产出酸碱度合格的烧结矿,以可靠、稳定、实用、提高生产力为原则,提供以下控制系统:
1、 配料混合系统
根据烧结工艺精准平稳配料、混合、加湿,达到合理的酸碱度和湿度
2、 烧冷系统
控制烧结料面、速度、破碎粒度、风温、负压及除尘
3、 筛分系统
根据筛分的粒度控制出料进仓及返烧,为生产数据统计,做好高炉备料
球团厂基础自动化控制
通过对从原料厂进到配料仓的干精矿、湿精矿、膨润土等原料进行配料、混合、造球、焙烧、冷却、输送、数据管理等自动化控制,为高炉生产粒度、酸碱度合格的球团矿。
炼铁厂基础自动化控制
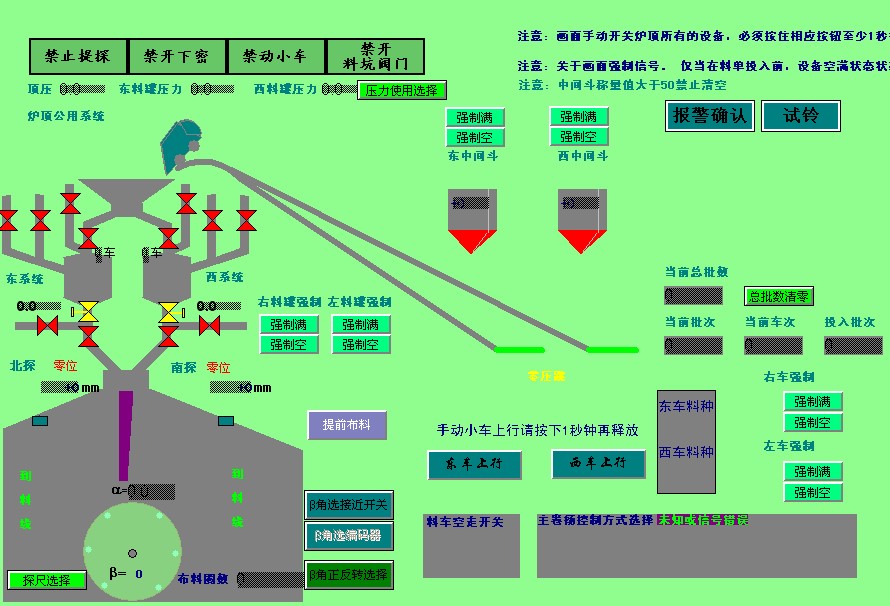
为高炉炼铁提供技术先进的自动化控制系统,实现了控制系统的三电(电气、仪表、计算机)一体化和管控一体化。
主要控制功能包括:
高炉矿焦槽系统控制
高炉上料系统控制
高炉炉顶系统控制
高炉本体及热风炉系统控制
煤气除尘系统控制
煤粉制备及喷吹系统控制
炼钢基础自动化控制
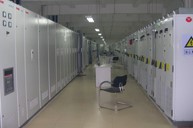
为转炉、钢包精炼炉、圆坯和方坯连铸机等冶炼主工艺线的自动化控制系统的集成和投运。其控制系统均实现了三电一体化。
转炉自动化控制技术
氧枪控制系统
倾动控制系统
加料控制系统
造渣吹氩成分微调升温控制系统
汽化控制系统煤气清洗及回收系统
连铸机自动化控制技术
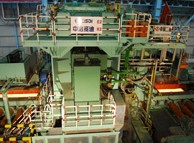
二冷水动态控制系统
优化切割控制系统
质量判定成品冷却堆放系统
公共水务、液压及称重系统
轧钢厂基础自动化控制系统\
热连轧三电集成控制技术,包括三电设备成套及热轧应用技术集成控制软件的的编制及调试。
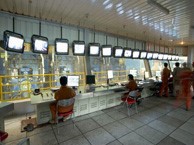
轧机自动化控制系统
速度主令控制
机架间微张利控制
机架间活套控制
飞剪剪切控制
冷床及精整控制
高炉卷扬控制
高炉上料卷扬系统是钢铁生产中的关键环节,主要作用是将生产所需的各种原料源源不断地送到高炉内,保证高炉的正常需要,而整个高炉上料卷扬系统的核心就是料车的主提升设备。
高炉上料卷扬系统特征:主卷电动机工作频繁,负荷重,启动转矩要求高。料车要求位置控制的精度高,系统的可靠性和安全性高。料车在启动和停车制动时震动大,要求电机工作的稳定性能高。
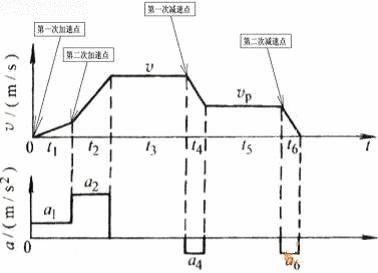
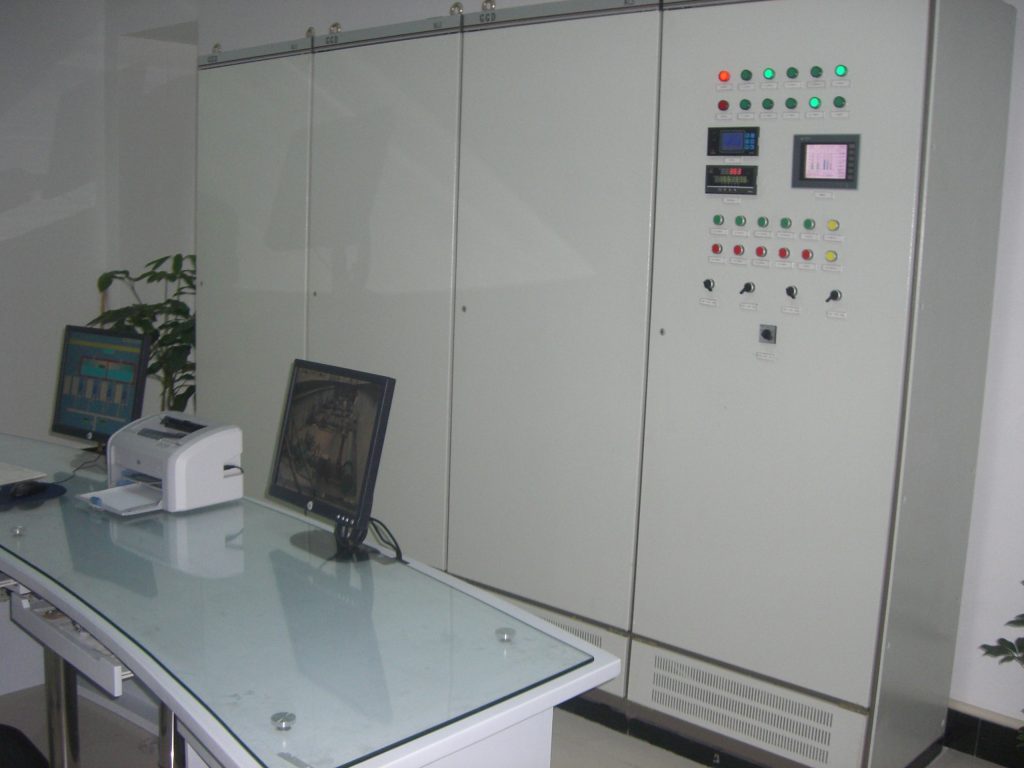
运行保护:
在系统将可能发生的故障和可能导致危险发生的情况的开关量进行串连汇总与一个零压保护回路中。在不出现任何状况下,零压回路为闭合状态,此时主回路接通,系统才可以正常工作。
对于料车运行中飞车失控的现象,采取低速检查保护措施。作为卷扬上料装置,采用速度闭环的方式,在低速的地方增加主令控制信号。
行车变频控制
传统行车均为串级调速加继电器/接触器控制方式,故障率高,维护费用及时间均很大,给生产造成不良影响,为此需对其技术改造,而采用变频调速控制很好地解决了主/闭钢丝绳受力平衡问题,软启软停方式大大降低了起制动时的冲击电流,再加上变频器本身具有完善灵敏保护功能,极大地提高了行车运行的可靠性,延长了系统的使用寿命。
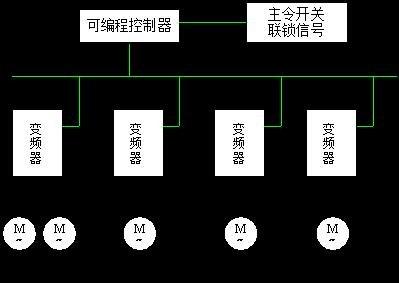
系统中选用了PLC来实现整个系统的逻辑控制,主要功能如下:
- 变频器启/停控制;
- 控制抱闸,保证电机轴停止时抱闸才抱住,既不提前,也不延后;
- 主卷变频器控制方式切换(速度控制/力矩控制)
- 系统安全连锁功能
a) 行车上各个进出口的门以及操作室的门在打开状态下,禁止操作。
b) 大、小车轨道两端设限位开关限制车体超越。
c) 冲顶限位
d) 各操作手柄未处于零位置时,上电被禁止。
e) 变频器中任意一台变频器报故障时,变频器均立即停止输出(自由停车),同时抱闸合闸。
f) 任何时刻断电,系统将立即停止,抱闸合闸。PLC故障时,各操作命令无效(PLC无输出),抱闸闭合,行车处于安全停止状态。一旦出现特殊情况,可按“急停”按钮,切断控制电源,使抱闸闭合。